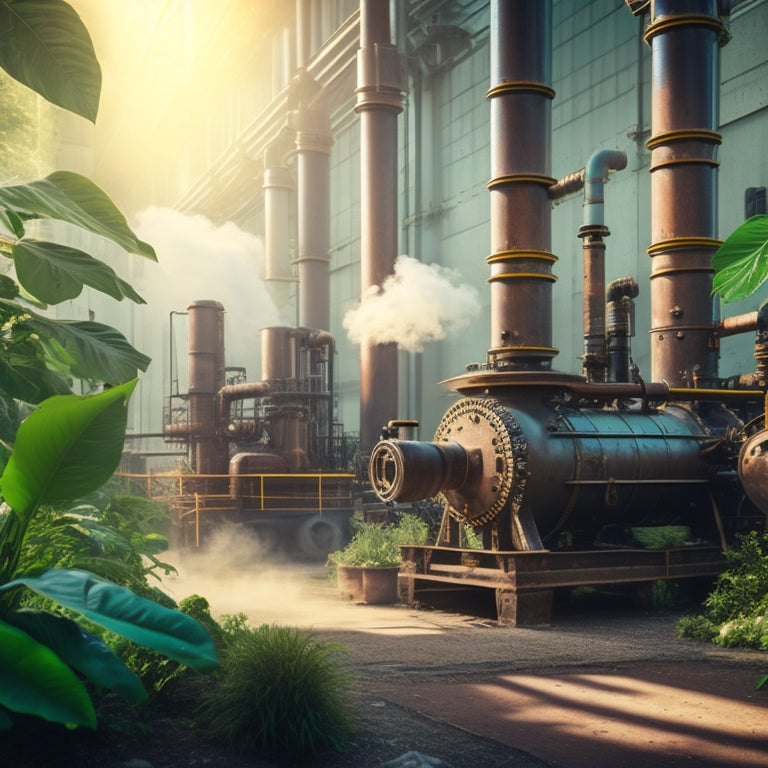
Steam Control's Role in Energy Efficiency
Share
Steam control plays a crucial role in enhancing energy efficiency within industrial settings. By monitoring steam usage, you can identify inefficiencies and implement targeted strategies that cut costs and promote sustainability. Investing in high-efficiency systems and conducting regular energy audits not only minimizes waste but also guarantees peak operating conditions. Properly sizing components directly influences steam performance and reduces energy expenses, while proactive maintenance extends system longevity. These practices collectively enhance operational flexibility and adaptability. If you want to investigate how these strategies can change your energy efficiency further, there's much more that could benefit your operations.
What You Need to Know
- Monitoring steam usage identifies inefficiencies, enabling targeted strategies that reduce costs and enhance sustainability in energy consumption.
- Proper sizing of steam components maximizes efficiency, reduces energy waste, and lowers operational costs, ensuring optimal performance.
- Advanced monitoring technology and data analytics facilitate real-time tracking, predictive maintenance, and informed decision-making to improve operational efficiency.
- Effective steam control reduces wear on system components, prolonging equipment lifespan and minimizing maintenance costs through proactive maintenance strategies.
- Demand response strategies enhance operational flexibility, allowing steam systems to adapt to fluctuating energy demands while promoting sustainability.
Optimizes Energy Consumption Effectively
To optimize energy consumption effectively, you must closely monitor steam usage across your operations.
By identifying areas of excess, such as inefficient steaming practices, you can greatly reduce energy waste and enhance overall efficiency.
Implementing targeted strategies not only lowers costs but also contributes to a more sustainable energy model.
Additionally, investing in high-efficiency steamers can further minimize energy consumption while still providing professional results optimizing steam production.
Monitoring Steam Usage
Effective monitoring of steam usage is essential for maximizing energy consumption in industrial settings. By leveraging advanced monitoring technology, you can gain understanding into steam flow and identify usage patterns that drive inefficiencies. Real-time tracking of steam consumption trends, combined with sensor integration, allows for proactive management of resources.
Implementing data analytics enables you to evaluate efficiency metrics and compare them against performance benchmarks. This analytical approach equips you to make informed decisions that enhance operational efficiency. Additionally, predictive maintenance becomes feasible when you can analyze historical data and detect anomalies, minimizing downtime and ensuring peak performance.
Here's a concise overview of these elements:
Monitoring Aspect | Benefits | Key Features |
---|---|---|
Steam Flow | Identifies inefficiencies | Real-time tracking |
Usage Patterns | Improves resource allocation | Data analytics |
Performance Benchmarks | Enhances decision-making | Predictive maintenance |
Reducing Energy Waste
Identifying inefficiencies in steam usage sets the stage for reducing energy waste and maximizing consumption. You can start by conducting thorough energy audits to pinpoint steam leaks and other issues that drain resources. Addressing these leaks not only curtails energy waste but also improves system reliability.
Implementing effective insulation techniques minimizes heat loss, guaranteeing steam remains at ideal temperatures as it travels through your system. Regular system upgrades can greatly improve efficiency, utilizing advanced technology integration to streamline operations.
Maintenance strategies are essential; they keep your system in peak condition and preemptively address potential failures. Training programs for your staff guarantee they're equipped with the knowledge to identify inefficiencies and implement solutions swiftly.
By establishing efficiency benchmarks, you create a clear standard for performance, allowing you to measure improvements effectively. This proactive approach enables you to make informed decisions that enhance your energy efficiency, ultimately leading to substantial cost savings and reduced environmental impact.
Embrace these strategies, and you'll not only improve the efficiency of your steam system but also champion a culture of sustainability within your organization.
Enhanced System Longevity
By implementing effective steam control measures, you greatly reduce wear and tear on your system components.
Just as dance floor mats with superior cushioning enhance performance and comfort, maintaining ideal operating conditions not only enhances performance but also extends the lifespan of your equipment.
Ultimately, investing in these strategies leads to greater reliability and lower maintenance costs over time.
Reduced Wear and Tear
Minimizing wear and tear on steam systems greatly improves their longevity, ultimately leading to increased operational efficiency and reduced maintenance costs.
When you implement effective steam control strategies, you enhance equipment reliability by reducing stress on components. This proactive approach allows you to anticipate potential failures rather than react to them, making preventive maintenance an essential practice.
You'll find that maintaining ideal pressure and temperature levels not only conserves energy but also extends the life of your equipment. By avoiding excessive cycling and fluctuations, you minimize the strain on valves, pipes, and other critical components, ensuring they operate smoothly for years to come.
Moreover, investing in regular inspections and timely repairs can drastically reduce the likelihood of unexpected breakdowns, which can derail your operations and lead to costly downtime.
You're not just preserving your assets; you're nurturing an environment where your team can work efficiently and confidently.
Optimal Operating Conditions
Achieving ideal operating conditions in your steam system is essential for enhancing longevity and efficiency. By focusing on precise steam temperature and effective pressure regulation, you can greatly improve performance. Control algorithms play an essential role in maintaining these parameters, ensuring that thermal dynamics operate at their best.
Incorporating energy recovery systems enhances overall efficiency metrics, allowing you to utilize waste heat and reintegrate it into your processes. This system integration not only elevates efficiency but also contributes to load balancing, reducing strain on individual components.
Implementing proactive maintenance practices is imperative. Regular performance benchmarking helps identify deviations from peak conditions, enabling timely adjustments. By addressing potential issues before they escalate, you can prolong the life of your steam system and maintain peak performance.
Ultimately, committing to these strategies cultivates a culture of operational excellence. You're not just investing in immediate gains; you're ensuring your steam system remains reliable and efficient in the long run.
Strengthen your operations by prioritizing ideal conditions, and watch your performance and energy savings soar.
Operational Flexibility and Adaptability
In today's ever-evolving industrial environment, your steam systems must exhibit operational flexibility to respond to varying demands effectively.
By implementing fluid system adjustments and demand response strategies, you can optimize energy usage while maintaining productivity.
Additionally, leveraging data analysis perspectives can help identify areas for improvement, ensuring that your operations remain efficient and responsive.
Embracing this adaptability not only enhances efficiency but also positions your operations for future challenges.
Dynamic System Adjustments
Fluid system adjustments are essential for enhancing steam control and energy efficiency in industrial operations. By implementing flexible adjustments, you can greatly improve system integration, allowing your steam systems to respond swiftly to varying operational demands. This flexibility is key in achieving peak performance and reducing energy waste.
You'll want to focus on performance benchmarking to identify areas for improvement. Regularly evaluating your system's performance against established benchmarks helps pinpoint inefficiencies and informs necessary adjustments. With real-time data at your fingertips, you can make informed decisions that enhance operational responsiveness.
Moreover, these adjustments promote adaptability in your steam systems, enabling you to shift operational parameters without major downtime or disruption. This adaptability not only supports energy efficiency but also allows you to maneuver changing production requirements with ease.
Ultimately, by prioritizing flexible system adjustments, you're not just improving performance; you're nurturing a culture of continuous improvement. Embracing this proactive approach allows you to utilize the full potential of your steam operations and drives sustainable energy practices.
Isn't it time to liberate your processes and maximize efficiency?
Demand Response Strategies
Demand response strategies are vital for enhancing operational flexibility and adaptability in steam systems. By implementing effective load forecasting techniques, you can predict energy demand fluctuations, allowing your system to respond proactively to changes. This not only reduces energy waste but also guarantees that you're optimizing your resources effectively.
Engaging consumers in the demand response process is equally important. When you actively involve them, they become more aware of their energy consumption patterns and can adjust their usage during peak times. This engagement cultivates a culture of efficiency, where everyone benefits from reduced energy costs and a more stable grid.
Moreover, adopting these strategies enables you to maintain control over your steam system, reducing reliance on non-renewable energy sources. As you enhance your operational flexibility, you gain the freedom to adapt to market demands and environmental regulations swiftly.
In a rapidly changing energy environment, demand response strategies aren't merely an option; they're a necessity. By integrating these approaches, you can guarantee your steam systems aren't only efficient but also resilient, laying the groundwork for sustainable growth and energy independence.
Selecting Based on System Size
When selecting steam control systems, proper sizing is essential to guarantee peak performance and energy efficiency.
An appropriately sized system can greatly reduce energy waste and operational costs, making it a key consideration for your facility.
Additionally, just as dance studio design requires careful planning for space and functionality, so too does the sizing of steam systems impact their effectiveness.
Importance of Proper Sizing
Achieving ideal energy efficiency in steam systems hinges on the critical aspect of proper sizing. When you select components that match the system's specifications, you optimize steam pressure and considerably enhance overall system efficiency.
If your steam traps, valves, and piping are too large or too small, you're likely to face inefficiencies that can lead to energy waste. Proper sizing guarantees that your system operates within its designed pressure range, minimizing the risks of overheating or underperformance.
Oversized components can cause excessive steam pressure, leading to higher energy costs and potential equipment damage. Conversely, undersized components may restrict steam flow, resulting in inadequate heating and increased fuel consumption.
In a world where energy independence is a growing concern, taking control of your steam system's efficiency is enabling. By investing the time to size your components correctly, you're not only reducing operational costs but also contributing to a more sustainable future.
Embracing proper sizing strategies allows you to maximize the potential of your steam system while enjoying the freedom of lower energy bills and reduced environmental impact.
Don't underestimate the importance of this critical step in achieving energy efficiency.
Impact on Energy Savings
Selecting the right components based on your steam system's size directly influences energy savings and operational efficiency. When you prioritize steam efficiency, you optimize energy use, leading to significant cost reduction. A well-sized system guarantees proper thermal regulation, minimizing energy waste and improving system performance.
By focusing on energy optimization, you can maximize the return on your investment while maintaining operational integrity. Oversized or undersized components lead to inefficiencies that not only escalate energy costs but also compromise resource management. Each component must align with your system's specific demands, allowing for effective sustainability practices that support both environmental goals and financial stability.
Moreover, accurate sizing of valves, traps, and controls promotes better steam distribution, which further enhances energy savings. This customized approach enables you to leverage the full potential of your steam system, guaranteeing that every ounce of energy is employed effectively.
Lower Operational Costs Overall
By optimizing steam control, you can considerably reduce energy consumption, which directly lowers your operational costs.
Embracing Makeup Basics for effective resource allocation can lead to enhanced system efficiency.
Implementing efficient steam systems not only enhances productivity but also minimizes waste, allowing you to allocate resources more effectively.
Ultimately, this strategic approach leads to a healthier bottom line for your business.
Reduced Energy Consumption
Regularly integrating steam control systems can lead to significant reductions in energy consumption, ultimately lowering your operational costs. By enhancing steam efficiency, you're not just improving boiler performance but also ensuring superior steam quality, which is essential for effective system integration.
Conducting thorough energy audits allows you to identify inefficiencies, providing a clear path toward optimizing your processes. Establishing energy benchmarks helps you gauge your current performance against industry standards, giving you a tangible reference for improvement.
This data-driven approach enables you to make informed decisions that encourage operational sustainability. For instance, a cost analysis can reveal how minor adjustments in steam control can yield substantial savings over time.
Additionally, a well-maintained steam system minimizes waste, reducing your overall energy consumption. By prioritizing these strategies, you're not only creating a more efficient operation but also embracing the freedom that comes from lower costs and reduced environmental impact.
You gain the power to control your energy use, enhancing both your profitability and sustainability. Ultimately, investing in steam control systems is a proactive step toward achieving your operational goals while promoting a more energy-efficient future.
Frequently Asked Questions
How Does Steam Control Affect Greenhouse Gas Emissions?
Steam control directly impacts steam efficiency, leading to significant emission reduction. By optimizing steam processes, you can minimize waste and greenhouse gas outputs, ultimately promoting a cleaner environment while maximizing energy use in your operations.
What Are Common Steam Control System Maintenance Practices?
Think of your steam system as a finely-tuned instrument. Regular steam trap maintenance and precise pressure regulation guarantee peak performance, preventing energy loss and costly repairs, allowing you the freedom to focus on efficiency and productivity.
Can Steam Control Systems Integrate With Renewable Energy Sources?
Yes, steam control systems can integrate effectively with renewable energy sources. By optimizing steam integration, you can enhance overall efficiency, reduce reliance on fossil fuels, and adopt sustainable practices, giving you the freedom to innovate and reduce emissions.
What Industries Benefit Most From Steam Control Solutions?
Imagine a lively factory floor; industries like chemical processing, food production, paper manufacturing, and textiles thrive on steam control solutions. You'll find enhanced efficiency and reduced costs, granting you the freedom to innovate and grow.
How Do You Measure the Effectiveness of Steam Control Systems?
To measure steam control systems' effectiveness, you evaluate performance metrics like energy savings, pressure stability, and response time. Optimizing these aspects guarantees you maximize efficiency, providing you the freedom to operate your systems effectively and sustainably.
Explore More
Incorporating steam control into your energy management strategy isn't just smart; it's essential. Think of it as the backbone of your system—supporting efficiency, extending longevity, and adapting to your needs. By choosing the right steam control solutions customized to your system size, you're not only slashing operational costs but also enhancing overall performance. Don't underestimate the power of optimized steam control; it's a game changer for achieving sustainable energy efficiency and operational excellence.
Related Posts
-
Elevate Your Style With These 3 Feminine Casual Wear Must-Haves
You're just a few stylish tweaks away from elevating your feminine casual wear from basic to breathtaking! Start by e...
-
Captivating Ballerina SVG Designs for DIY Enthusiasts
Ballerina SVG designs have captured the interest of DIY enthusiasts and crafters, providing a versatile and sophistic...
-
Issuu's Dynamic Flipbook Creation: Engage & Share
Issuu's dynamic flipbook creation platform revolutionizes digital content creation, offering an intuitive and seamles...